- FläktGroup
- Solutions
- Operating Theatre Ventilation
Operating Theatre - Clean Room Ventilation
During an operation human life must be safeguarded to avoid contamination from the surrounding area.
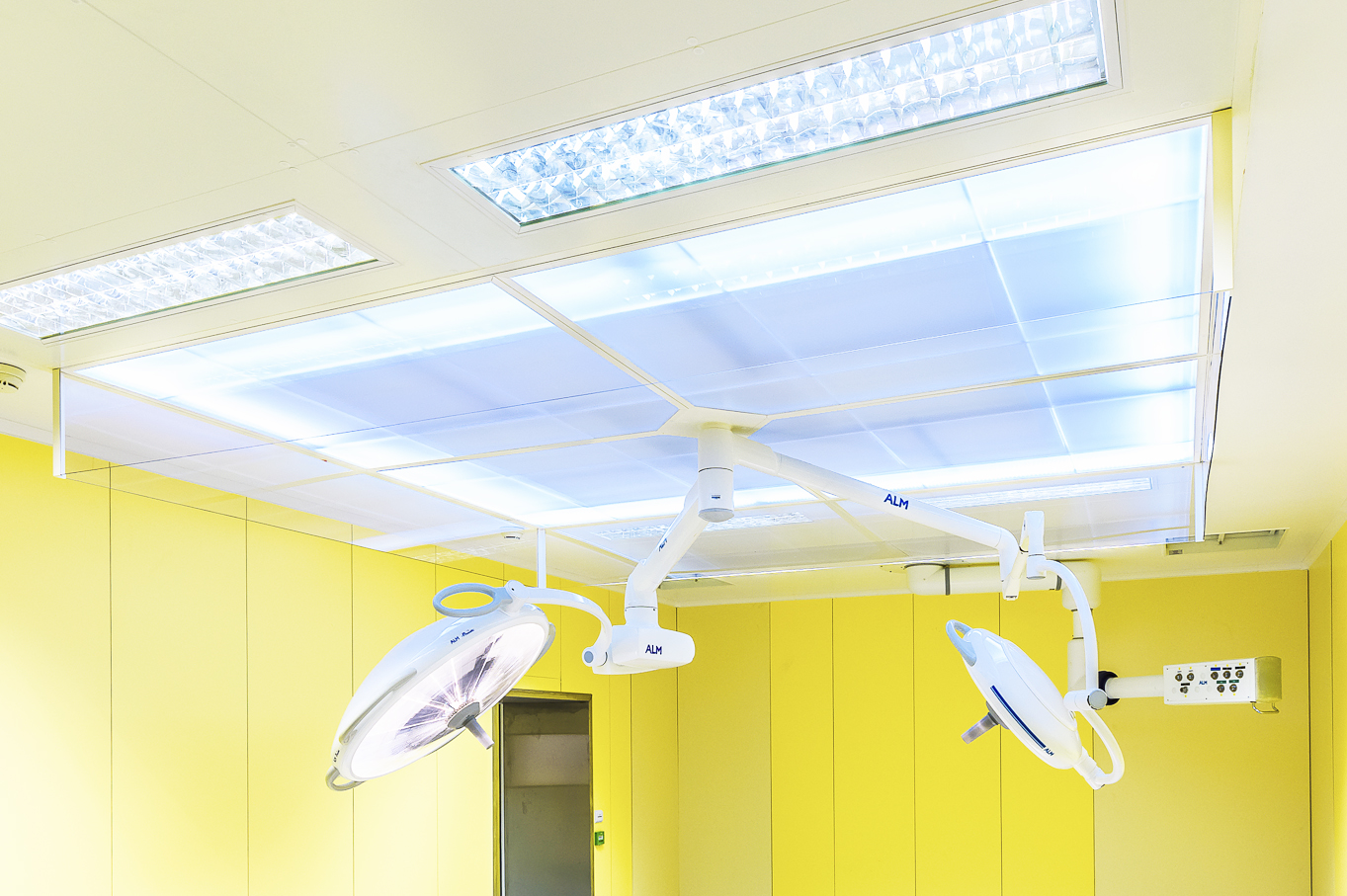
Safeguarding human life at it's most vulnerable
To understand HVAC solutions within an operating theatre we must first be aware of the varirty of risks. Our specialist hospital ventilation solutions have been developed to meet the specific needs of this application type.
During an operation contamination can come from 2 main sources.
- Engogenous, which essentially comes directly from the patients skin or body matter; or from an infected prosthesis or implant.
- Exogenous, which comes from the surrounding environment or surgical staff and their equipment.
The understanding of the above leads us on to consider such things as direct and indirect contamination. Direct meaning items that will directly be place in contact with the patient during surgery such as surgeons hands and instruments. Indirect is therefore contamination which might come from dust in the air, droplet nuclei, even the fibres in clothing or airborne infectious diseass.
Contamination Control
- Supply air needs to be filtered in three stages with a HEPA filter at the third stage
- Low turbance airflow above the operating table (almost laminar)
- Overpressure to the neighbouring rooms needs to be maintained at ca. 15Pa
- All surfaces inside of the room should be smooth and easy to clean – rounded corners, reduced numbers of joints
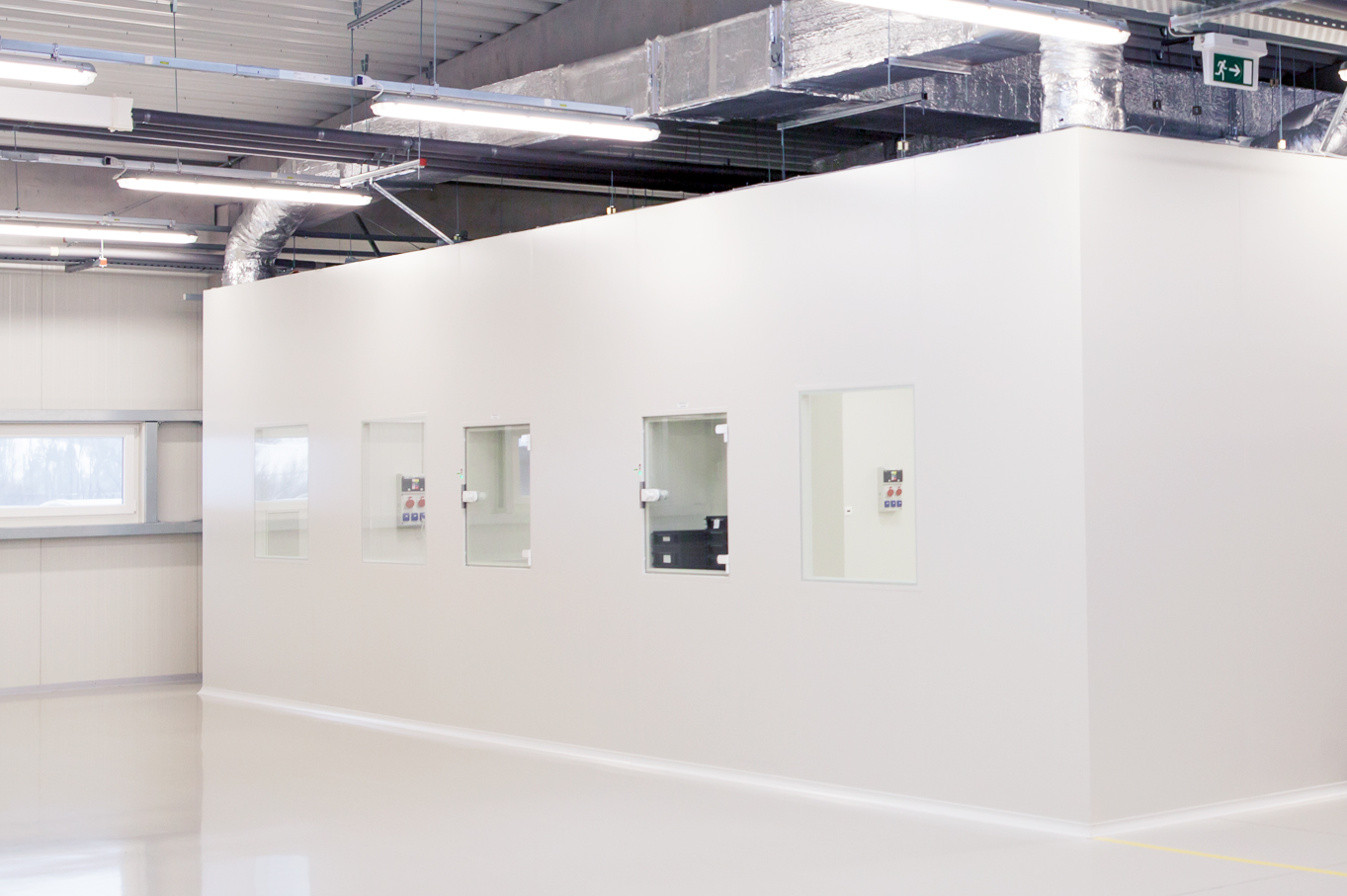
Clean Room Technology by FläktGroup
Numerous international manufacturers work with FläktGroup‘s Clean Room Technology as a result of our expertise in developing reliable and effective contamination control methods for Clean Rooms.
Clean Room solutions from FläktGroup permit users to coordinate all critical parameters precisely with the requirements of respective production processes and to systematically control decontamination of room air. These solutions control air pressure, temperature, and moisture – especially the contamination with fine dust, skin particles and bacteria – and keep these contaminants away from products and processes.
Effective and precise clean rooms design is essential for semiconductor production and pharmaceutical industries, as well as companies in the chemical industry, space technology, and optics and laser technology perform research and production; where we see that conditions in these industries are increasingly relying upon Clean Room conditions.
Technical, chemical, and biological quality products with highly sensitive manufacturing processes are further processed in hermetically sealed areas that demand room air that is virtually dust-free. The manufacturing process itself, however, requires ambient air absolutely free of particulates.
Our Process
We offer a full portfolio of support every step of the way from 3D design to installation, to reports in order to develop your bespoke project.
1. Consultation
With decades of experience in clean rooms, we bring the necessary expertise into your project and help you to create an optimal concept for the clean room, which is energy efficient and reliable.
2. Detailed Design
Once the clean room layout is finalized, we create a 3D model with all little details – to the last screw.
For you to check – and for our production.
3. Production
All our factories work with the 5S approach and have a best-in-class on-time delivery rate.
In our modern facilities we produce fast standardized products, but are flexible to support you with customized solutions.
4. Installation
The installation is a crucial part in the process. Especially for a clean room. Hence, we have very well trained teams in our core countries. Everywhere else, a supervisor from the factory will be present during the whole installation phase.
5. Validation
We support the finalization of your project by bringing in our long-term partners. You will get a full report, which is complying to all global and local regulations and standards. And – of course – you can be ensured, that your clean room will operate as required.
Products
-
Fresh Heaven MAXX O POWER LAMINAR AIRFLOW UNIT
- Complete filtration of operating area with a function to mix supply air (from AHU) and recirculating air
- Easy installation, maintenance and disinfection
- Low initial pressure drop of HEPA filters
- Tailored dimensions with LED lighting and control unit
-
Fresh Heaven MAXX O LAMINAR AIRFLOW UNIT
- Complete filtration of operating area
- Easy installation, maintenance and disinfection
- Low initial pressure drop of HEPA filters
- Tailored dimensions with LED lighting and control unit
-
CGx Ceiling Air Outlet HEPA FILTER DIFFUSORS
- Used in pharmaceutical industry, laboratories, hospitals, microbiology, electronic industry, and food industry
- Easy integration in all types of FläktGroup suspended ceilings
- Filter classes H13 to U15 in an aluminum frame, with dry or fluid seal
- For turbulent displacement flow
- Integrated pressure-gauge connection for monitoring pressure drop
- Tube for applying test aerosol (measuring of concentration)
-
SANDWICH PANELS
- The panels have a sandwich structure (two steel sheets with thermal insulation between them), with painted or stainless-steel sheet facing
- Custom colors and various core options are possible with minimal particle release
- R-panels 62 mm thick, M-panels and Me-panels are 60 mm thick
- Matching flush glassed-in panels (non-opening windows) and doors are available
- All joints are sealed by permanently elastic silicone in a color closely matching the panel color
- Round connections to the floor, suspended ceiling, and inner corners (Radius profiles system) are available
- The panels offer easy maintenance, effective sanitation, and resistance to disinfectants
- They ensure tightness to maintain over pressure or under pressure in the clean room
-
Inwall FACINGS
- The ideal solution for adapting existing rooms into clean rooms.
- Easy and quick fixation to structural walls
- All panels are prefabricated – minimal adjustments on site
- All joints sealed with silicone
- Panels connected via conductive cables are grounded to the earthing point
-
DOORS & WINDOWS
- An automatic drop-down seal integrated into the door leaf enhances the air-tightness of a door
- Being flush with sandwich wall partitions ensures easy maintenance and flawless disinfection
- An interlock system equipped with signaling units prevents both doors in an airlock room from being opened simultaneously, effectively reducing the risk of contamination
- Doors can be opened manually or automatically with automatic drive
- Transfer doors are used as partitions of transfer boxes (passive or with filtered airflow)
- Accessories available include automatic drives, door closers, mirrors, windows with sunblinds, windows made from float glass or safety glass (ESG, VSG), automatic drop-down seals, stainless-steel kick plates, electromechanical and electromagnetic locks, signaling panels (semaphore), and many more.
-
EXHAUST-AIR COMPONENTS
- Reliable ventilation of anesthetic gases, particles and exhaust of room air burdened with microbes
- Various choices of extract-air components
- Seamless integration of extract-air components in all types of wall panels and facings
-
CEILINGS
- LS ceiling – clip-in light ceiling
- KS ceiling – grid cassette ceiling
- KSH ceiling – walkable Alucore grid ceiling
- RS ceiling – walkable sandwich panel ceiling.
- A minimum number of particles is released from the panel surface
- Ease of installation, cleaning and sanitation, resistance to conventional disinfectants
- Joints between cassettes are sealed using permanently elastic sealant
-
GLFC 0604-1204 BD2 (153 – 326 kW)
- Version with 4 scroll compressors
- SEPR-HT values up to 6.1
- 13 models in ErP 2021 compliant design to EU 2016/2281
- Versions available as Standard or Super Silent execution (SL)